Cold forming and Industry 4.0
24 April 2020
By Jerry Bupp, vice-president of sales and marketing, National Machinery LLC
Technology and the way information is handled today is changing rapidly. The use of analytics and data is everywhere, from the team owner trying to find the best athlete to fill out his team, to an executive in the automotive industry determining forecasts and risks of product recalls. As we learn to use information better, we can improve our daily lives. That can also translate to manufacturing efficiency in our production facilities.
A key concept for those in manufacturing has been Industrial Internet of Things or Industry 4.0. The idea is based on the next (or fourth) industrial revolution, the trend towards automation and data exchange in manufacturing technologies and processes. Many times people think of it as having a ‘smart factory’. It can be easy to understand the overall concept, but difficult to put into practical terms, until we dive into the details and some examples. Simply put, the goal is to collect, store, analyse and present data that is relevant to a machine’s performance.
National Machinery has added features to its base FORMAX® cold forming machines to make sure they are Industry 4.0 prepared and also expanded, and added new, features/sensors – taking users to another level of true Industry 4.0 functionality. To help visualise the possibilities, let’s review some key areas that can be enhanced by applying Industry 4.0 concepts to an advanced cold former such as FORMAX.
What information is available? There are two main types of data to review – economic and process data. Economic data is defined as machine production monitoring, while process data is defined as the machine condition and part forming monitoring.
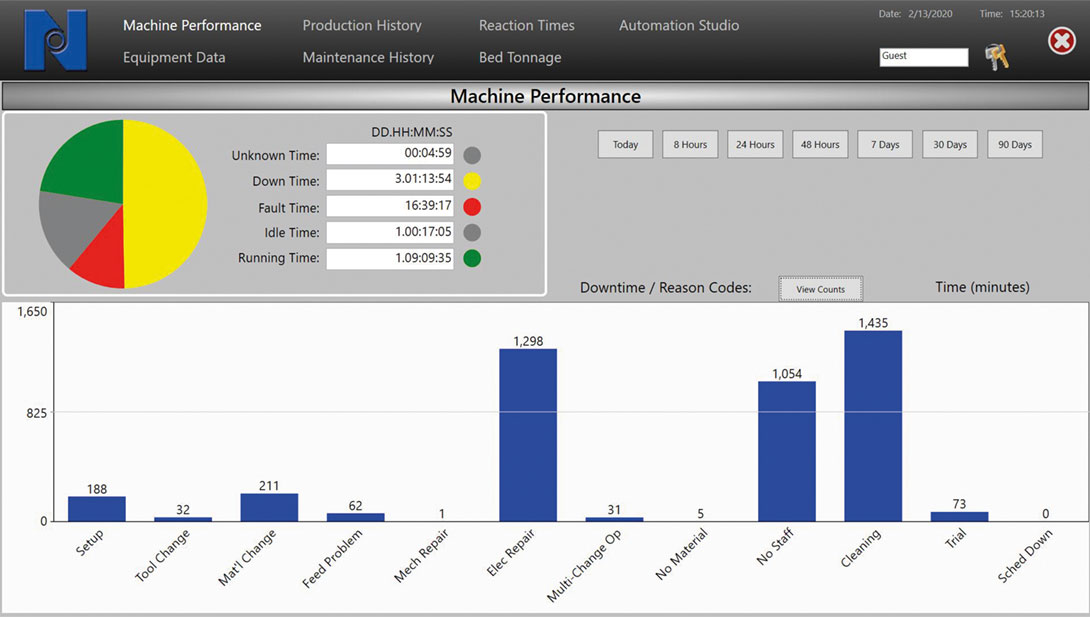
We can break those types into specific groups to help explain how to link Industry 4.0 to the cold former:
- Energy management: This data includes current and historical electrical power usage along with compressed air. As we know, both power consumption and pressurised air are very valuable resources. By monitoring their usages, an auto-shutdown of idle devices can be enacted, to allow for savings.
- Connecting systems with servers or the cloud: This is real time data available by OPC-UA, which is machine to machine communication unified architecture. This allows for connection to a manufacturer’s network and the ability to remotely view information. Utilising the cloud for data storage allows the information to be accessed how users wish by who they choose. Remote access to machine: A VPN connection allows for support and software updates through direct connection to the machine. This is a valuable tool to support a machine in the field, to minimise downtime.
- Automatic detection of machine errors: This can be an array of condition and position sensors that are utilised to monitor the machine and operator functions. Functions include drive motor amps, breaker bolt condition, pressures of fluid and the levels of those fluid reservoirs. Monitoring of the feed length is also possible.
- Monitoring product quality: Comparing the current and previous production runs of part tonnage is a way to both validate the current set-up and monitor the current part run. The regular scheduling and input for part inspection requirements also falls under this category.
- Performing predictive machine maintenance: Keeping the machine in peak condition is critical to making good parts and maintaining high production speeds. A full list of operator and maintenance tasks can be created, along with prompts such as warnings or reminders to ensure those tasks are completed. Preventative maintenance tasks can then be shown on a completion log to capture the history of when completed.
- Supporting machine commissioning/production: Information including operator manuals and parts catalogues can be made available on the machine’s touch screen for better convenience. Additionally, for the maintenance group, all the machine schematics (pneumatic, hydraulic and lubrication) are easily accessible along with detailed torque charts to help the operator with daily functions on the machine.
- Visualising machine conditions: The ability to have various sensors to give operators information is great, but sometimes you need a clear and visual representation of the status or warning. The Industry 4.0 machine interface sends pre-emptive prompts for items such as adding die coolant. It also allows users to view the current statuses of different aspects of the machine such as machine fluid levels. Industry 4.0 takes it a step further by not only providing beneficial alerts but by stating the causes for particular issues, for example warning that the oil cleanliness is an issue due to contamination or that there is excess moisture/water content in the oil. This type of data analysis can greatly benefit tool life while driving down production costs.
- Monitoring overall equipment effectiveness: What causes down time? This type of data collection shows how much time is spent in production compared to idle or down time. Various idle time reason codes can be used to decipher the cause of the machine stopping and then that data can be summarised into an analysis. This information can allow a production manager to target key reason codes and make improvements that will increase available production time.
- Managing machines and systems: This is the tracking of the job status, for example – recalling the set-up from the last time a job ran on the machine. This system can also track how many parts have been made in the current lot run and when the predicted completion will be of that lot, so one can prepare for the next changeover sequence. The operator is also given various ways to assist on improving production with automated adjustments (such as feed and kickout), digital readings of important job set points, counters for the punch and die tooling components, and push button machine position settings. Maybe there is an operator on a different shift that is more comfortable in another language; they can easily toggle between various languages to minimise any miscommunication of information and data.
- Monitoring machine conditions: Monitoring the performance of various machine components can help ensure high uptime availability. The ability to monitor the brake and clutch performance characteristics, along with monitoring the hydraulic system seals, are all steps to keep the machine in good working condition.
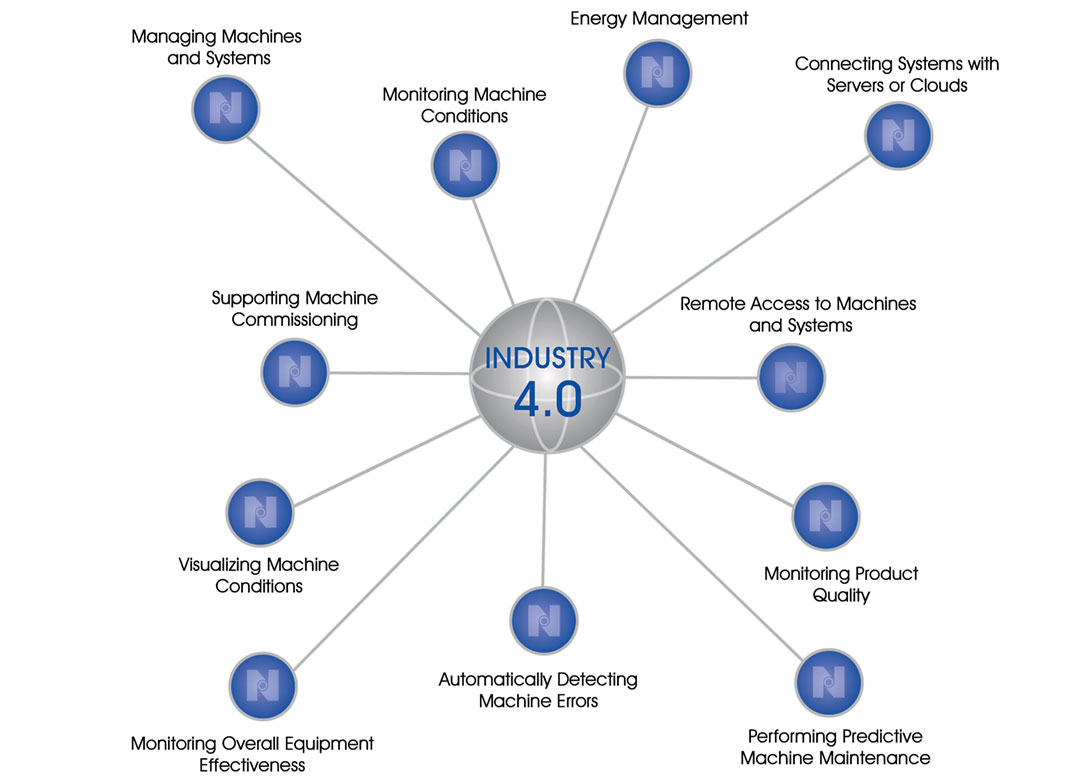
These features can now all be realised on a new FORMAX machine from National Machinery. Customers can choose to add a load monitor of their choice, but it’s not required as an interface to make this system and features functional.
As one can see, there are many possibilities about how data and information can be used to improve production efficiency. In the case of a new machine from National Machinery, the base machine option comes with many of the listed systems to make it Industry 4.0 prepared. If a user sees the advantages of having more data, then additional sensors can be added into a full Industry 4.0 option on the machine. That feature would include all of the systems and data collection/analysis that is listed above.
The world is changing and data is at the heart of that change. Those that choose to truly use that data can take advantage of the knowledge to improve whatever they apply it to – the ability to score another goal, optimise a car design or get another hopper of parts from a cold former at the end of each shift.
www.nationalmachinery.com