The expansion and renovation of Non Standard Socket Screw
07 June 2016

Non Standard Socket Screw Limited (NSSS), based in Birmingham and London, has announced the extension of its Birmingham headquarters; the installation of an upgraded heat treatment facility and further production machinery – including an additional Cincom CNC sliding-head lathe; as well as the continued investment in infrastructure, process and quality.
After demolishing a recently purchased adjacent property, NSSS has extended its current premises by a further 8,000 square feet (approximately 743m²) and enlarged the site’s total floor area to more than 30,000 square feet (approximately 2,787m²). This new extension has been used to increase both its considerable stock range and self contained manufacturing facilities. The addition of further CNC lathes and expansion of raw material stock has now also been made possible.
A prime improvement in NSSS’ manufacturing capability will be a total upgrade of its current in-house heat treatment facility with the installation of an atmosphere controlled Ipsen TQ4 sealed quench furnace, temper oven and post heat treatment wash facilities.
NSSS has a policy of continuous improvement in all areas of the business. Its range of VMC, automatic and CNC lathes, and its associated computerised software, with turning capabilities between 2mm – 64mm are constantly under review and upgraded. This ensures both maximum efficiency and cost-effective production.
The company’s hot forging section has 5 presses with two blow capabilities of between 45 tonnes and 120 tonnes and the ability to forge from 5mm up to 36mm diameter – with lengths up to 760mm – as well as the associated imperial equivalent sizes. The hot forging process has the advantage of maintaining preferential grain flow for improved product quality and maximisation of strength. On set-up, all batches of work have the induction pre-heating of the blanks closely controlled using calibrated pyrometers, which ensures uniformity of temperature to specified settings and freedom from potential ‘overheating’ with its subsequent problematic material grain problems.
Close tolerance sizes for either pre-thread rolling or finished shoulder diameters are produced by precision CNC turning or centreless grinding on the thread rolling section. The finished thread form on fasteners can be manufactured by either profile turning or thread rolling and NSSS has the capability to produce by both methods. The thread rolling section carries an extraordinary range of thread rolls in both metric and imperial sizes including Whitworth, BSF, UNC, UNF, BA and many other obsolescent thread forms that many customers now find difficult to obtain. The thread rolling capability can produce sizes as small as 8BA to 1¼ inches, again with their associated metric equivalents.
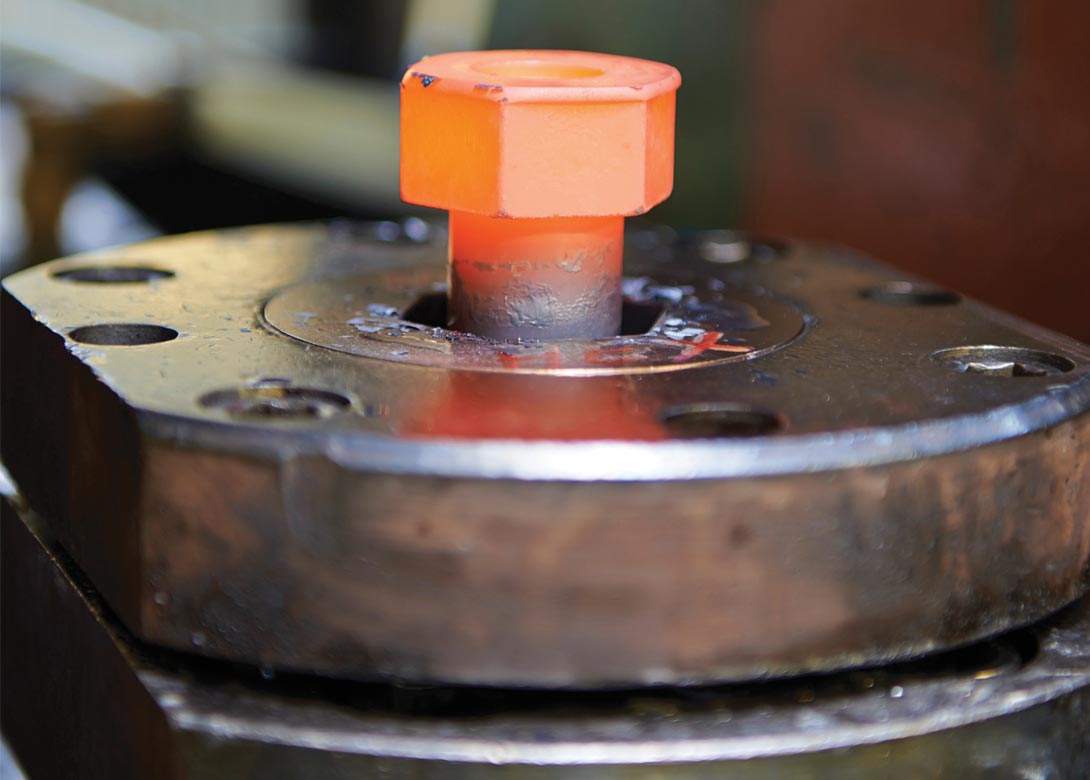
The quality control department makes continuous improvements in manufacturing records, methods and techniques to ensure product quality remains central to the ethos of the company. As well as its extensive range of calibrated gauges and other measuring equipment, the company has invested in a Keyence IM-6120 optical measurement device, which has the ability to simultaneously measure a number of workpieces and store the information for statistical analysis, future reference, and evaluation. This device will enhance the current quality checks in place, which include at least five independent checks by quality control and twelve checks by responsible operators. A recent purchase of further digital hardness testing equipment for the heat treatment department also ensures continued compliance and repeatability for the post-machining heat treatment processes. This dedicated approach to quality helps to ensure that all products meet the customers’ expectations.
Since its foundation in 1971, NSSS has continued to develop as both a major stockist of standard fasteners and a manufacturer of other fastener products from either individual customer drawings or reference samples in a large variety of materials. These include alloy and stainless steel, brass, bronze, duplex, titanium, and a vast range of other exotic alloys. The company’s self contained manufacturing facilities have the capability to produce parts by a range of different processes in sizes ranging from a miniscule 8BA to 64mm diameter in both metric and imperial specifications. Whether it’s a ‘standard’ product from stock or a ‘non-standard’ product to be manufactured, NSSS has the capability to supply.
“NSSS offers an open invitation to all customers to come along and visit its impressive manufacturing facility where they will receive a guided tour of the premises and may even witness their orders being manufactured right before their eyes. From bar to box to you, Non Standard Socket Screw delivers.”