SARIV focuses on Industry 4.0
06 February 2017
In such a changing and competitive environment, many companies are deciding to look at the opportunities and challenges of Industry 4.0. One such company is Italian-based SARIV Srl, which has been using its S.I.MES (SARIV Integrated Manufacturing Execution System) to digitalise its production process.
Here Nicola Satore, managing director at SARIV, talks about why SARIV – a manufacturer of blind rivet and rivet nuts – decided to introduce S.I.MES and what the benefits have been since its introduction.
What is the SARIV Integrated Manufacturing Execution System?
“S.I.MES is an IT platform that deals with planning, quality, tests, efficiency rates, and files, and manages all the information and material flow in the company’s recently extended production plant in Fontaniva, in the north-east of Italy.
Using WiFi connections, visual signals, as well as PC and PLC screens nearly everywhere across SARIV’S two production plants, the system has almost eliminated the need for paper. Indeed, paper has been completely removed for the tests in production and in the laboratory, and every measurement is made through connected test equipment. This means that all the measurements and material flows are archived into one big database.
Every single bit of production data is now immediately available, from simple production controls in laboratory measurements, to SPC process data analysis, as well as the collection of all information on the production process, including every single batch, for example feedback on tests or the reason for any process interruption.
Our aim was to deal efficiently with the increasing complexity coming from producing different parts for different fields, such as industrial and automotive, as well as customised parts. These fields required different levels and frequency of controls, but needed to be produced and tested in the same production plants, with the same operators.
Also, in recent years there have been a lot of changes at SARIV, including the acquisition of the Israeli company Self-Fix in 2014.
When we acquired Self-Fix we moved its machinery to the plant in Italy to increase the capacity in manufacturing structural rivets. That is also why we increased the production site from 5,000m2 to 8,000m2 at the beginning of 2016.All of this has enabled us to grow the number of products we offer to nearly 2,000, and above all, has brought an increase in production capacity.”
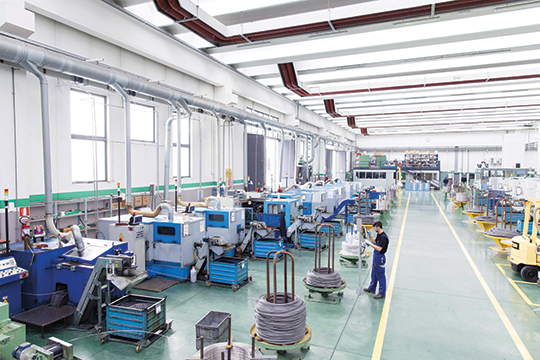
In 2016 a new factory brought the SARIV production site from 5,000m2 to 8,000m2
Why did you decide to introduce the S.I.MES?
“We are speaking about a system that has connections everywhere – production, quality department, laboratory, and R&D. The intention was not to make any compromise, and to design and develop a system that was tailored to our needs.
The first steps of designing S.I.MES were long and hard, and a complete analysis was mandatory and very useful to understand where we could start to improve. Now, after nearly four years from the start of the project, we know it was a turning point for us. We are enlarging the activities of S.I.MES, by working on the tool department to include it in the system.
If asked to describe what S.I.MES meant for us, I would say it is a facilitator, as it absorbed with its IT technology the complexity of the production process. Now, I think it means even more for us. It’s not only an instrument, it’s one of the main reasons why we are growing at this rate.”
What have been the benefits of introducing the system?
“Digital tools have become more important to businesses, causing significant changes in the way we communicate, work and trade. This has given rise to new challenges and opportunities, and has activated the digital transformation of enterprises.
As we are a manufacturing company, and the design and all production steps – including galvanising – are carried out internally, the production department is our main action field and focus.
That’s why monitoring and controlling an increasing number of machines has become fundamental to get more data from the processes, to improve process controls, and to ensure that processes operate at their full potential.
This trend is continuing with an ongoing investment in machinery and equipment to enlarge the capacity of SARIV’s production of tools, which are used in the various steps of production.
In this phase of the company’s development, we are sure that the S.I.MES was and is decisive in letting parts and information flow easily in a context where the complexity is constantly growing.
We have increased nearly 40% our production capacity since 2014, and most of this capacity was filled with new projects, new tests, new materials and new requirements. Dealing with it in the ‘old’ way would have been extremely hard, S.I.MES was the best solution to rely on.”
What have been the main challenges of running the system?
“Now the challenge is all about dealing with the huge amount of data available on the system – including interruption causes, delay reasons, process modifications and so on. There is so much data that the biggest aim is to find the key data that is important for SARIV.
In order to do so, we needed to improve our business intelligence capabilities; our know-how in data analytics; and to give our operators adequate training. This will enable us to collect the so called ‘big data’ and to analyse it to find the ‘right data’.”
What improvements will there be for your customers?
“This digital transformation and the internal changes have given us the opportunity to speed up the manufacturing process for every product, so lead times in supply have been significantly reduced.
Moreover, we can instantly monitor the production phases of every single product, knowing in real time what part is being assembled or what treatment it is undergoing. This enables us to have a clear vision on the actual manufacturing process.
Finally, all of our quality system is integrated on the same IT platform of S.I.MES, meaning that all the data connected to a specific lot is stored in the database. We can therefore supply much more information on every single solution we offer, from the technical design, to the laboratory analysis, to the final tests.
This is valid for every kind of customer, from the ‘simple’ distributor to the most complicated application, such as in the automotive sector.”
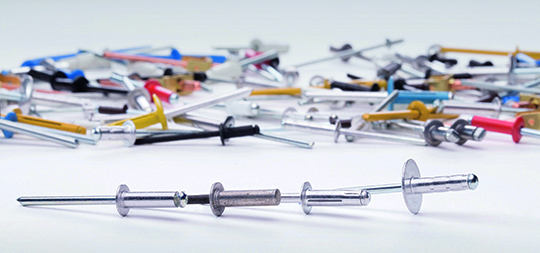
3 million rivets and blind rivet nuts are manufactured every day for the most important automotive producers on the market
How does S.I.MES help you when dealing with the automotive sector?
“The automotive sector is our biggest challenge. Product consistency, quality, and reliability, are more and more important to decrease the risk of faulty parts.
The change from a testing protocol based only on operators to a system that ‘guides’ the operators and manages what test measurements have to be done and when – collecting automatically all this information – has decreased the risk in a sensible way.
Having all the measurements on databases means having SPC data available in real time, helping us to discover deviations and drifts before the product goes out of tolerances.
Everything is moving faster, and such a digital base – with all this kind of data – is mandatory for us now, influencing all our decisions and actions.”
www.sariv.it