NSSS continues major investments
05 June 2017
Following the 8,000 square foot extension to its Birmingham headquarters last year, Non Standard Socket Screw Ltd (NSSS) is pleased to report on further major investments carried out as part of its ethos of continual improvement in all areas of the business – ensuring it continues to meet the various requirements of its wide range of customers and guarantees its commitment to both product quality and customer satisfaction.
An increase in floor space has enabled NSSS to expand in all areas of both the warehouse and its manufacturing facility. These, along with the expertise and ongoing training of personnel in all areas of the business, have ensured maximum technical capability and good teamwork.
NSSS already has a well known reputation for its fully self-contained manufacturing facility, with the ability to produce parts to customers varied and exacting requirements, but the recent significant investments have further enhanced these capabilities.
The company’s already extensive range of Autos, CNC and VMC facilities have been further improved and extended with the recent purchase of two new Citizen CNCs. The Cincom L20 and L32 seven-axis, sliding-head, automatic lathes have the capability to produce parts up to 32mm diameter and 600mm length. Both machines are fitted with the latest HD automatic bar feeds, automatic swarf control, inbuilt fume extraction and fire suppression equipment – giving the capability of a lights-out manufacturing facility if required. As always, NSSS’ CNC computer software and programmes are continually monitored and improved to ensure optimisation of both product quality and machine efficiency.
As well as its Autos, CNC and VMC capabilities to turn or mill bar, NSSS has a large range of hot forging machines with two-blow capabilities of between 45 tonnes and 120 tonnes. These have the ability to forge from 5mm up to 36mm diameter with lengths up to 700mm, including the imperial size equivalents. Product quality is maintained and the risk of overheating prevented during the induction heating process using a pyrometer temperature-measuring gauge.
Following either forging or CNC turning, products are thread rolled and can be supplied in a vast range of thread types and sizes. These include sizes from 8BA to 1½ inch (including metric equivalent) in metric, Whitworth, UNC, UNF, BA, BSF and many other either current or obsolescent thread types, or sizes that many customers may now find difficulty in obtaining. Larger thread sizes can also be achieved by thread cutting.
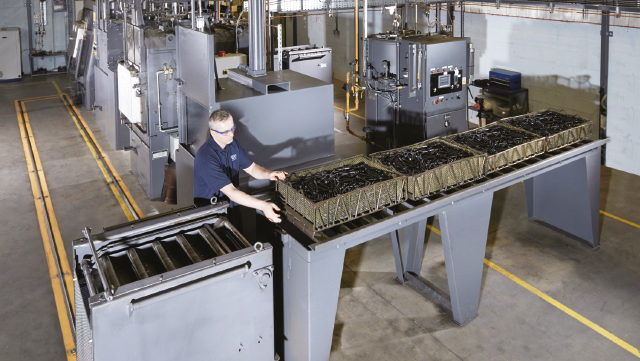
Following the final machining operation, products are heat treated to the final required strength grade. This is now carried out using the recent significant investment in an Ipsen TQ4 sealed quench furnace and its associated auxiliary equipment. This equipment, with its close temperature uniformity and computerised endothermic atmosphere control, ensures that product integrity is maintained at all stages of the heat treatment operation. These controls retain surface carbon potential, freedom from oxidation and scale – with minimal hardness variation within the batch. All batches of heat treated products are checked using the latest digital Rockwell hardness testing machine.
Throughout all areas of production, product quality is paramount and the dedicated quality team oversee this by ensuring strict controls and measurements are carried out at all stages of manufacture. Their extensive range of calibrated gauges and other measuring equipment ensure quality compliance is maintained during all process operations. In addition, a Keyence IM 6000 optical measuring device has the ability to simultaneously measure a number of items and store the information for statistical analysis, evaluation and future reference.
If required, some products can be supplied with independently tested metallurgical reports such as mechanical testing and chemical analysis to 3.1.