Organisational changes at CFA
06 June 2017
For any organisation to develop and grow, it needs to embrace change. The Construction Fixings Association (CFA) is no exception, and has recently made positive changes to the structure and personnel of the association.
The Construction Fixing Association is a non-profit organisation made up of seven full members who represent the largest manufacturers and suppliers of anchors and fixings in the UK. The organisation also incorporates Associate Distributor members and Approved Tester members, who – as members of the CFA – reflect and promote the high standards of the organisation.
In early 2016, the very experienced and eminent Mark Salmon left his position as general manager having devoted 20 years to the CFA. The contribution that Mark Salmon made to the CFA and the anchor industry in the UK was very significant, and he is a loss to the association.
At the point of Mark Salmon’s departure, the board of the CFA took the opportunity to review the CFA’s place in the market and assessed the association’s needs through to 2020.
In replacing Mark, the CFA created two new roles and appointed an external consultant to take over secretariat duties.
The new roles created are a technical manager, plus a commercial manager. In the recruitment for the two new roles the CFA has managed to secure the specialised service and 50+ years of experience of two stalwarts from the world of construction fixings.
The role of technical manager has been taken by John Muir and that of commercial manger by Andrew Thomas. Both will provide dedicated coverage to these functions, but will also a provide flexible approaches to the overall association activities. John Muir has 40 years experience in the construction industry, 25 years of which was specifying and designing anchors. Andrew Thomas has a background in mechanical engineering and spent over 12 years as technical lead with a leading global fixings manufacturer, having previously been involved in anchor manufacturing.
These changes constitute an investment by the CFA to provide a greater level of support to the industry through more direct contact and improvement to all CFA services. This also allows the CFA to provide a more proactive approach to the industry stakeholders.
What will not change, however, is the key objective of the association, which remains to ‘“ensure best fixings practice” by raising the standards of quality and safety in all aspects involving the selection and installation of safety critical fixings.
The CFA, for many years, has promoted the exclusive use of products with ETA certifications and will continue to do so. The integration of anchor design into Eurocodes, with the imminent introduction of EN1992-4, will further strengthen the design standards for anchors. Involvement in European and UK technical committees will also continue, ensuring that the UK’s interests are fully represented.
In recent years, since the introduction of BS 8539:2012 ‘Code of practice for the selection and installation of post-installed anchors for concrete and masonry’ the CFA has focussed its attention in driving best practice and raising awareness through this code.
It is important to remember that this code of practice came into being due to the increased number of high profile anchor failures, which had occurred in recent years. With CFA’s involvement in the BSI committee, which drafted this document, there is now a best practice model for all stakeholders in the industry – providing clear roles and responsibilities for all these functions.
The CFA provides detailed support to these roles, principally through the CFA website, which has been updated and revamped in recent months. The website provides a BS 8539 Toolkit that includes extensive information on all aspects of the code, and for all roles, as well as guidance notes, technical articles and installation method statements.
Further developments, which will be introduced in the near future, will include online webinars and installation videos – allowing access for a wide audience to the CFA training and educational material.
What is clearly a key issue in the selection and installation of anchors, is competence, and that is competence at all levels and across all functions in the process. In looking at the reasons for anchor failures, there are some key areas that need to be addressed on a competency basis:
- Inappropriate anchor selected: Specifiers need to be able to not only design the anchor, but assess the other selection factors that apply. Then the selected anchor should be fully specified in detail, to avoid ambiguity in procurement.
- Anchor specification changed without approval: Changes in specification must be made correctly with
full compliance to the equal and approved status, and in line with the code.
- Anchor incorrectly installed: The contractor must have competent supervisors and employ competent
installers. The installers must be trained, and competent with the knowledge required to follow manufacturer’s instructions and using correct setting tools.
Bearing these points in mind, having a means to provide the skills required to overcome these issues has become the priority for the CFA. To achieve this, the CFA has put in place a comprehensive seminar and training programme for all stakeholders.
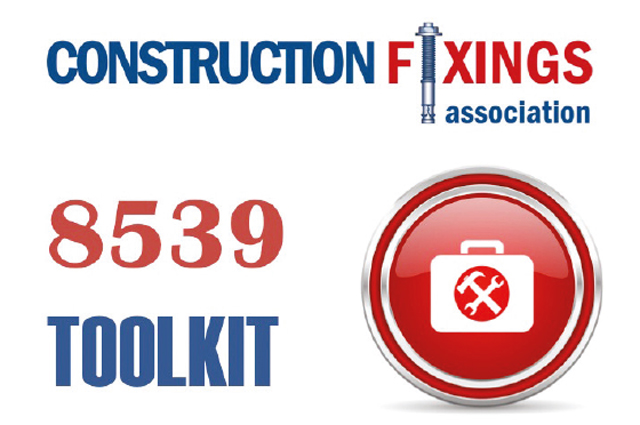
CPD can provide seminars on a wide range of anchor subjects including BS 8539, anchor design, and anchor technology, which are being delivered to clients, specifiers, contractors and installers.
In addition, the CFA Academy provides a programme of certified competency training courses. These include installation, anchor testing (proof & advanced) and supervisor courses, which are run on a regular basis and provide compliance to BS 8539.
To ensure that anchors with the appropriate level of approval are readily available across the UK, the CFA has spent over 8 years building a network of Approved Distributors across the UK, all of which have received training and instruction in the correct selection and specification of fasteners and can provide full technical support in-line with the manufacturer and code guidelines.
These Approved Distributors can provide on-site support to the manufacturers standards. At the start of 2017, 25 Approved CFA Distributors had been appointed to provide nationwide coverage.
Working in parallel with the Approved Distributors, a network of Approved Testers is also incorporated. All CFA Approved Testers have the equipment and skills to safety test all manner of construction fixings safely. Once tester accreditation is issued all members undergo ongoing assessments to ensure the highest standards are maintained, and that all test equipment meets industry calibration requirements. Moreover, all testers will be familiar with the requirements of the test regimes incorporated into BS 8539.
In summary, the CFA – being the leading authority on anchors in the UK – will continue to provide a constantly improving high-level of support and advice to the industry.